Phone: (346) 337-0714 Email: info@lynxTNM.com Lynx Test and Measurement LLC
AI Enabled Defect Recognition System
Our AI defect recognition system utilizes deep learning technology to accurately identify complex defects with 100 times higher accuracy than the human eye.
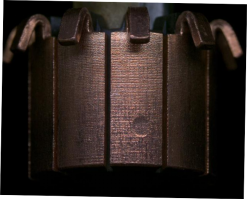
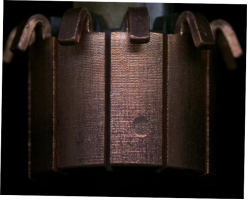
Improve quality inspection consistency with our defect tolerance classification management system, allowing for independent control of acceptance tolerances for different defect types.
Enhance quality control processes by classifying and managing defects after recognition, providing statistical results for improved decision-making and operational efficiency.
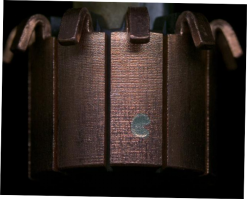
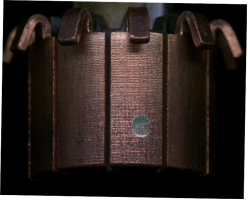
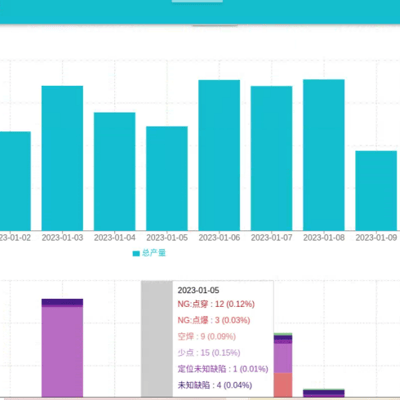
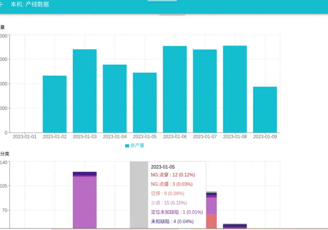
Frequently asked questions
What is AI Generated Defects Detection System?
The system is a fully automated loading and unloading defect detection equipment 100% in-line detection of more than 50 types of defects using Al enabled image recognition and deep learning system to identify defected testing material (parts and components) and provide statistical analysis for process improvement or management reports.
How does your product/service work?
We offer turnkey solution for your application. All system sold is included with a minimum of 8 hours of on-site setup and training while additional service and training can be purchased. When allowed in certain countries, extended warranty can be purchased at the time of the contract.
How much does it cost?
Our pricing varies depending on the size of the testing material and the speed of the output. We offer a variety of options to fit your needs and budget as low as US$10,000. Please visit our [pricing page/contact us] for more information.
What makes the Intelligent Imaging System so unique?
There are a total of 240 different lighting methods, fully adapted to the different types of defects lighting requirements. With typical exposure time is less than 0.25ms, the system is performing high-speed flying shooting.
How can I contact you?
You can reach us by [phone number/email address/contact form link]. We are always happy to answer your questions.
Where can I learn more about you?
You can explore other sections of this website, such as the "About Us" page or our blog, to learn more about our company, mission, and team.
Case Studies
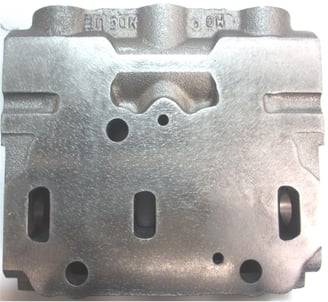
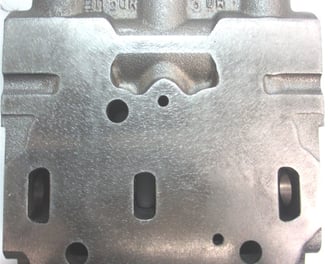
Testing Subject: Machined Valve Block
Partial defect types: Scratches, knocks, foreign objects, rust, burrs, etc. on the machined surface of the valve block.
Inspection challenges: Product processing surface is highly reflective. The differentiation of the acceptable grinding marks and the unacceptable scratches is difficult.
Detection solution: Deploying Robot Arms to grip the product for flying photography. There is a total of 3 combinations of exposure utilized with a 5MP camera, and a series of fixed focus telecentric lens to complete the picture. The resulted Inspection time is 10 seconds per piece.
Case Study 1
Partial defect types: O-Ring Quality Check in need of detection of appearance defects such as burrs, missing material, cracks, bulges, etc.
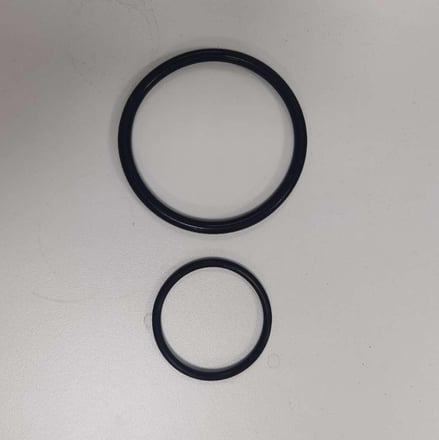
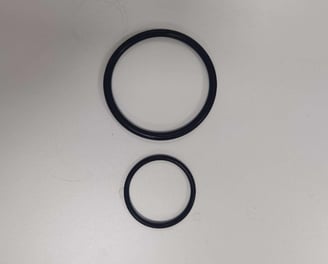
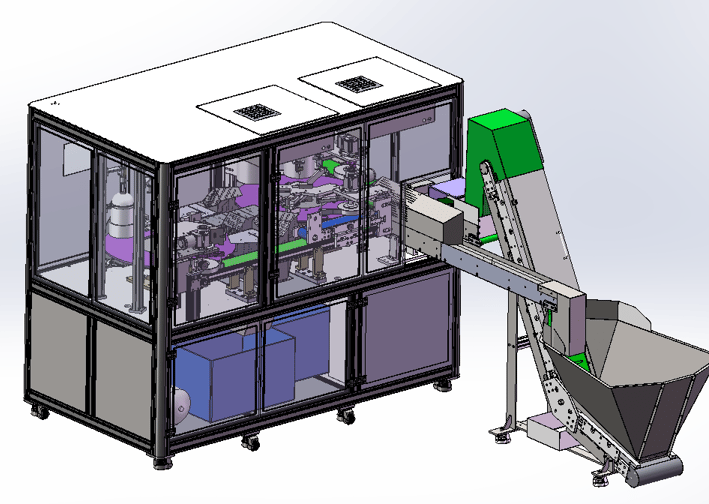
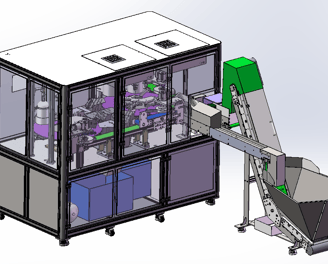
Case Study 2
Inspection challenges: Both surfaces and the inner and outer faces of the O-rings must be inspected.
Detection solution: Utilizing 11 sets of 2D cameras to inspect outer and inner diameters. The resulted Inspection time is 2 to 5 pieces per second.
Testing Subject: O-Rings
Here's what our customers say
”Every day, they strive to improve their service to the clients by developing the right blend of technology and creativity to make sure every job done is done as efficiently as possible.”
- Caterpillar
”Every day, they strive to improve their service to the clients by developing the right blend of technology and creativity to make sure every job done is done as efficiently as possible.”
- Brian Moten
Important
info@lynxTNM.com
Connect with Us
+1 346 285 3477
9207 Country Creek Dr. STE200
Houston, TX 77036
www.lynxTNM.com